For the past 10 years, Eco-Tech Ceram has been offering tailor-made, sustainable and cost-effective solutions to improve energy efficiency and recover waste heat from industry.
Tegulys
Tegulys, a tile and brick manufacturer in the Haute Corrèze region of France, needs heat to power its dryer and firing process. However, more than 50% of the heat consumed in the baking oven is lost. With theEco-Stock®it’s possible to capture and store waste heat from the baking oven, so that it can be used at the right time in the dryer and pre-bake chamber.
Aware of the economic and environmental profitability of such a project, the Nouvelle Aquitaine region andADEME have subsidized part of the infrastructure. Our network of partners then enabled Tegulys to finance the rest of the infrastructure via a financial lease.
Consult the technical data sheet
“We are the first industrial site to have welcomed the Eco-stock® solution developed by the Eco-Tech Ceram company in 2019. The trust and support of the New Aquitaine Region were decisive in validating the merits of this solution and customizing it. Finally, we are doubly satisfied: the Eco-Stock® solution allows us to improve the energy efficiency of the firing process but also to increase our production capacity.”
-Nicolas Ducrot, CEO of Tegulys
wienerberger
As part of their commitment to decarbonization, Wienerberger, a giant in industrial bricks and tiles, has decided to form a partnership with Eco-Tech Ceram.
The Pontigny site (Yonne – Burgundy Franche Comté region) is equipped with a thermal accumulator, our Eco-Stock®to transform heat loss into sustainable solutions.
Our thermal accumulator recovers the heat from their ovens to send it back to the dryers. The result is a reduction in energy consumption at their tile factory of over 480 tonnes of CO2/year, equivalent to more than 3.5 million km per year for a normal car.
It was commissioned in early 2024.
Consult the technical data sheet
“ With its Eco-Stock® solution, Eco-Tech Ceram will allow us to recover waste heat from the six Pontigny kilns and to use this waste heat in our dryers. Enabling Wienerberger to use 100% waste heat for drying its roof tiles, all the while eliminating 100% of natural gas consumption and achieving carbon-free drying.. “
– Robert Lacroix, Director of Sustainable Development, Wienerberger France
ArcelorMittal
ArcelorMittal is one of the largest steel producers in the world and the Dunkirk site represents one of the largest production capacities in Western Europe. Wishing to play its part in the fight against climate change by reducing its CO2 emissions by 35% in Europe by 2030, the company is committed to numerous energy efficiency initiatives at its industrial sites in France.
Our prototype has shown the profitability of our solution for the recovery of waste heat for the drying of agglomeration sludge. This means that ArcelorMittal does not need to use fossil fuels to dry its sludge, and no longer has to pay the extra cost of transporting wet sludge.
Consult the technical data sheet
“The work carried out with Eco-Tech Ceram enabled us to identify and prioritize several solutions for recovering waste heat: for sludge drying, and for steam, hot water and electricity production. Eco-Tech Ceram also provides a network of third-party financiers and financing solutions. The first Eco-Stock® was commissioned in April 2022 at the Dunkirk site.”
– Thierry Poirier, Head of Energy Department, ArcelorMittal France
Villeroy & Boch
Villeroy & Boch has chosen to surround itself with committed players in order to bring about a real environmental and energy transformation of its production facilities at Valence d’Agen. The manufacturer then prepared a comprehensive multi-year decarbonization program.
The technology we’ve implemented has significantly reduced gas consumption and CO2 emissions at the plant’s two biggest consumers. The company is aiming to save 8 GWh on its annual energy consumption, thus avoiding the emission of 1,400 tonnes of CO2 per year (global scope for the entire site).
Consult the technical data sheet
“The plant will thus reduce its gas consumption by 42% compared with 2021. Without this saving, the site would be threatened by rising gas prices.”
– Laurent Santarelli, Manager of the Valence d’Agen plant, Villeroy & Boch France
H2020 SME Instrument
The main objective of this project is to demonstrate theEco-Stock®our solution for recovering waste heat by thermal storage, in a real-life environment on a European heavy industry production site. To this end, the Eco-Stock® is installed in real conditions on an industrial site: Villeroy & Boch in Valence d’Agen, the international ceramics giant. It is directly adapted to the specifications of the tunnel furnaces of the site.
The Valence d’Agen plant has embarked on a genuine environmental and energy transformation of its production facilities.
This solution solves one of the major challenges facing industry today: increasing energy efficiency while reducing CO2 emissions and saving money.
Consult the technical data sheet
“We produce ceramic products, a material that lasts over time thanks to a traditional know-how internationally recognized for its manufacturing quality. We had to quickly start our energy transition in order to make this noble material compatible with the ecological challenges to come. Manufacturing in France, in a sustainable way, in synergy with local actors, skills, and resources will make Villeroy & Boch a model of Social and Environmental Responsibility! “
– Laurent Santarelli, Manager of the Valence d’Agen plant, Villeroy & Boch France
MITIGAT PROJECT
The MITIGAT project, financed by theEuropean Commission’s Innovation Fund Small Scale, aims to create a multi-energy platform for testing the following applications on an industrial scale:
- Heat to Heat
- Heat mobility
- Power to Heat
- Heat to Power
- Power to Power
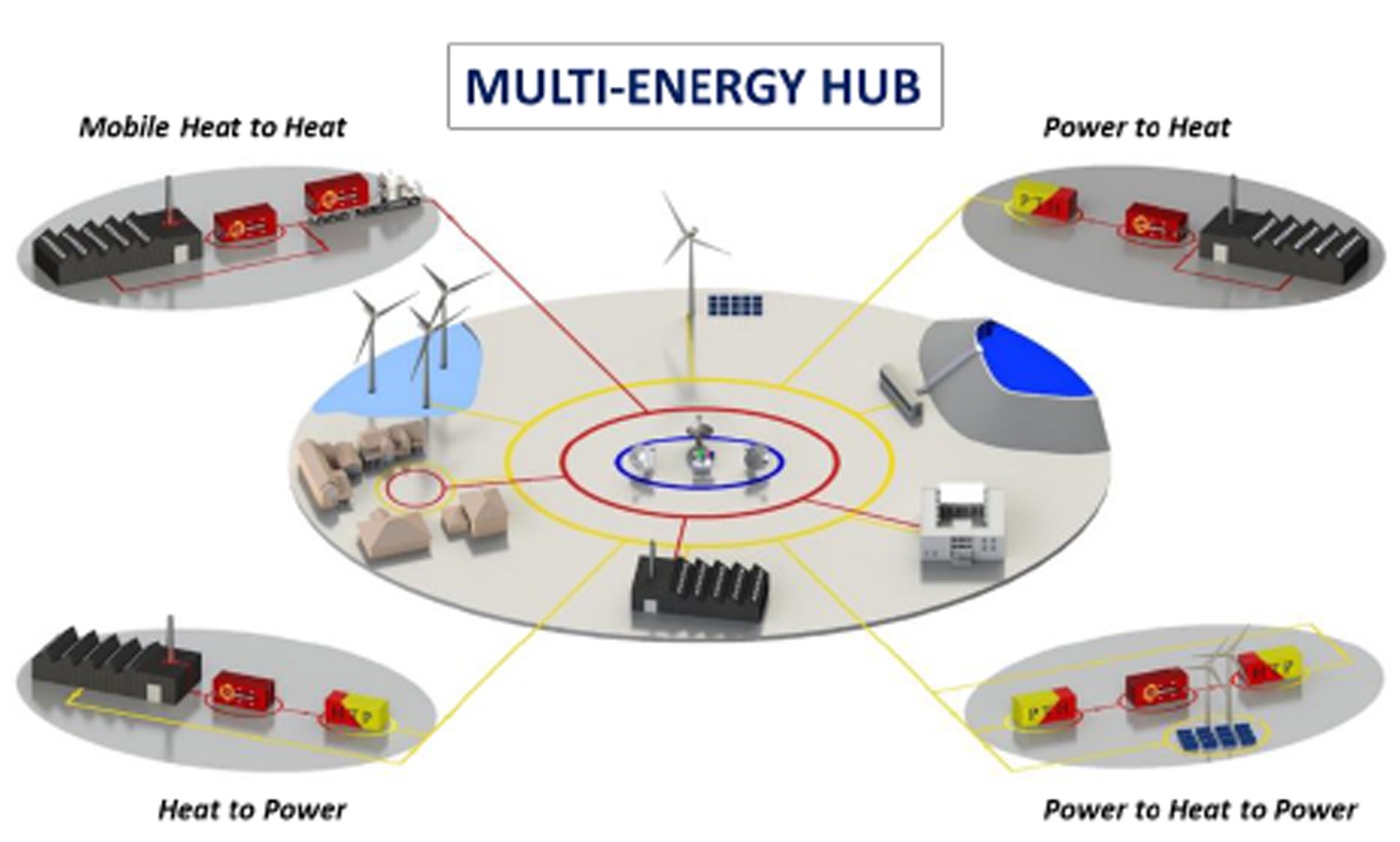
Aubert & Duval
In 2018, Aubert & Duval, a giant in high-end metallurgy, established a decarbonization strategy.
The goal? Reduce their greenhouse gas (GHG) emissions by 45% in 2030 (123,000 tons of CO2 equivalent emissions). After five years, they needed to find other levers and turned to Eco-Tech Ceram.
The project? Hot fumes from the metallurgist’s furnaces will be directed to a heat exchanger. With it, hot air will be produced which will feed the burners. As a result, the manufacturer expects to reduce CO2 emissions from its gas furnaces by 20-25%.
“We have already reduced our emissions by 39%, but with the mitigation of the pandemic and the jolts in aviation, we expect to see some pretty significant upturns in activity. To meet our decarbonization trajectory, we need to go much further! That’s why we turned to Eco-Tech Ceram, a company that specializes in energy efficiency.”
– Frédéric Pidoux, Head of the Environment, Energy & Industrial Risks Department at Aubert & Duval France
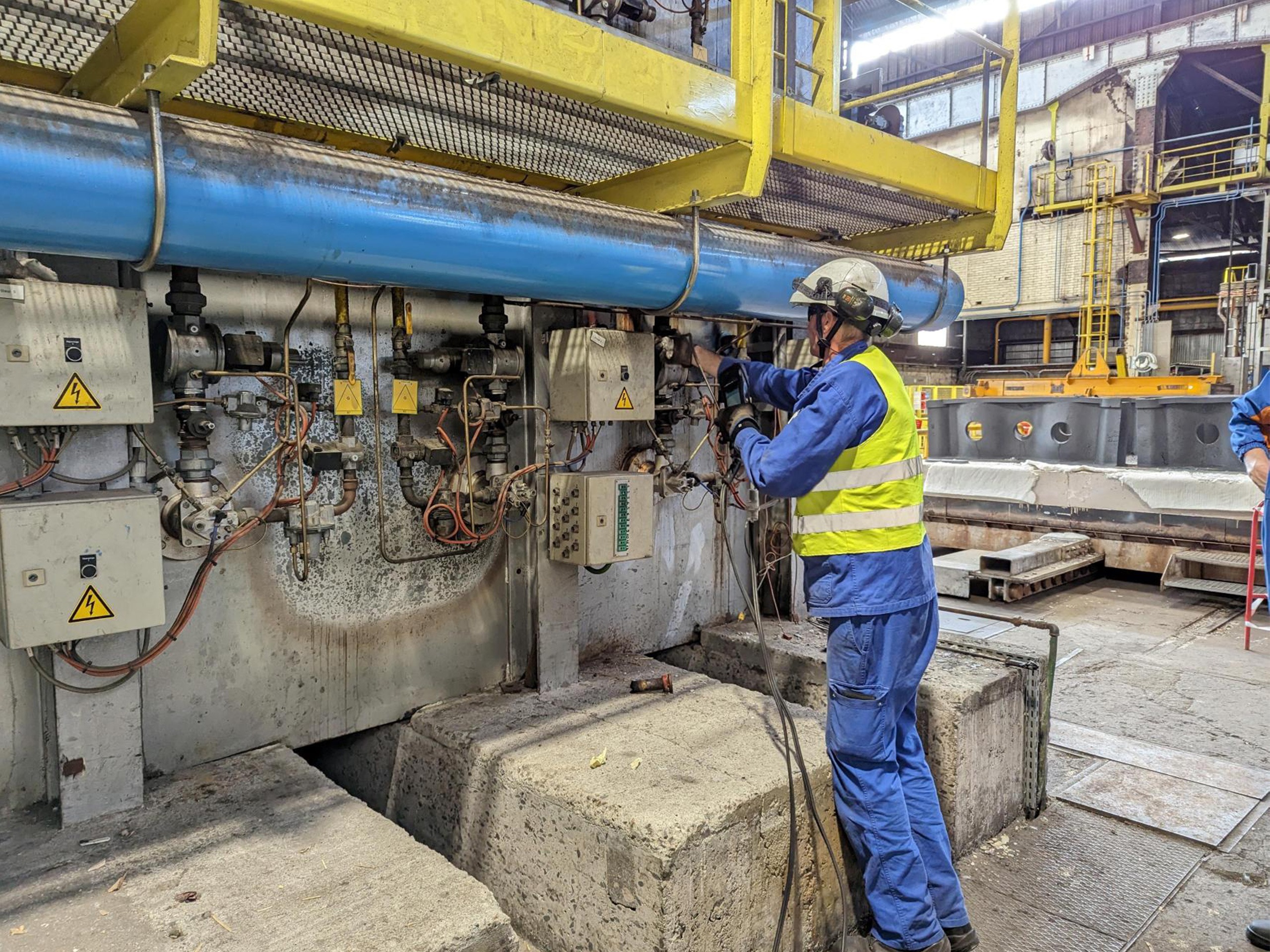
All our references
MITIGAT Project – Innovation Fund Small Scale
Eco-Tech Ceram, one of Europe's pioneers in thermal storage and waste heat recovery (SME phase 1 & phase 2), wanted to implement a multi-energies smart grid which responds to the dual constraints of intermittent waste heat and intermittent renewable energies.
Multi-technology storage platform
Prototyping - Storage/retrieval and multi-energy platform
High-temperature test bench
Prototyping - Production of a turnkey, high-temperature, mobile test bench
Waste heat recovery from kilns on dryers
Ceramics - Optimization of waste heat from 6 kilns of a unit producing more than 95% of the site's output.
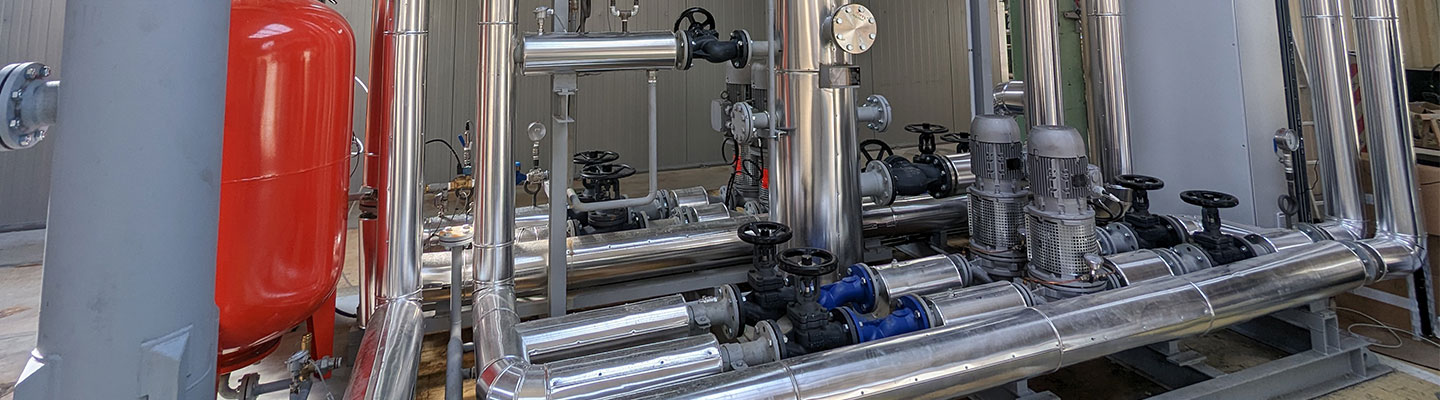
Waste heat recovery and energy optimization
Ceramics - Renovation of the plant's dryers, recovery of the compressors' waste heat and insulation of the slip and glazing tanks.
H2020 SME Instrument phase 2
Prototyping - Eco-Tech Ceram has been selected by the highly competitive H2020 SME INSTRUMENT PHASE II PROGRAM
Mobile waste heat recovery solution
Prototyping - Development of a 360 kwh fully containerized, mobile and modular pilot storage unit
Heat recovery via heat exchanger
Metallurgy - Recovery of waste heat from furnace fumes to preheat water used by the process boiler via a fume/water exchanger.
Global Innovation Competition
Prototyping - Development of eco-designed thermal storage units for energy transition and waste heat recovery.
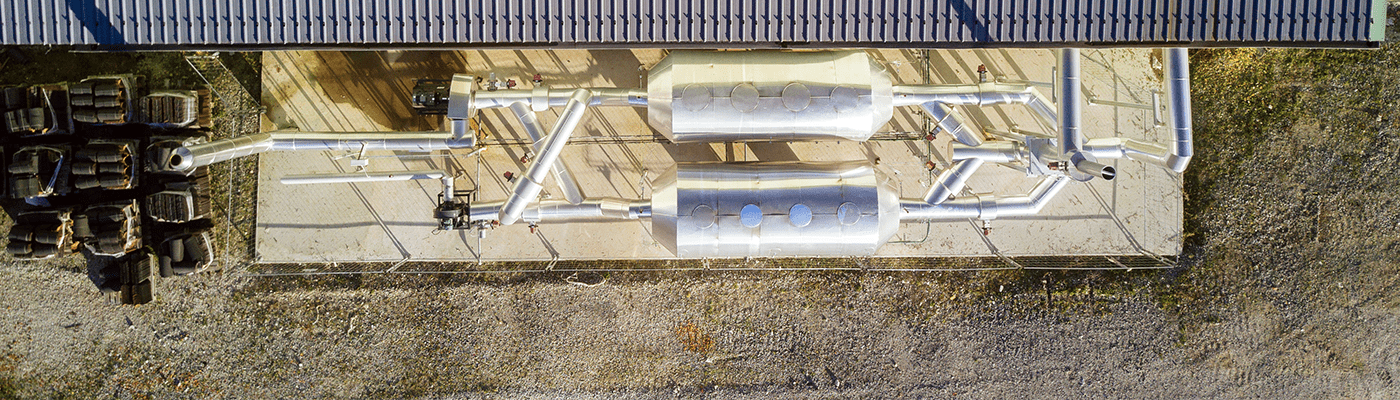
Recovery of waste heat from the kiln to the dryer
Ceramics - Recovery of high-temperature waste heat from a kiln for use in the plant's dryer - Tegulys

Fatal heat recovery study on a hot enclosure
Metallurgy - Replacement of preheating chambers using electric hot air guns by an exchanger and an Eco-Stock®.
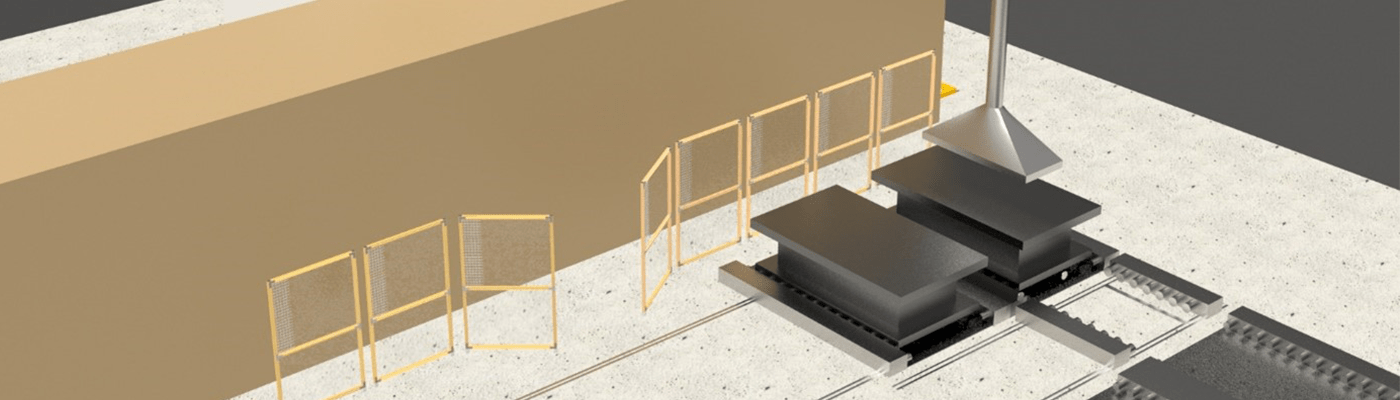
Improving energy efficiency in a foundry
Metallurgy - Energy optimization of the different zones of a foundry
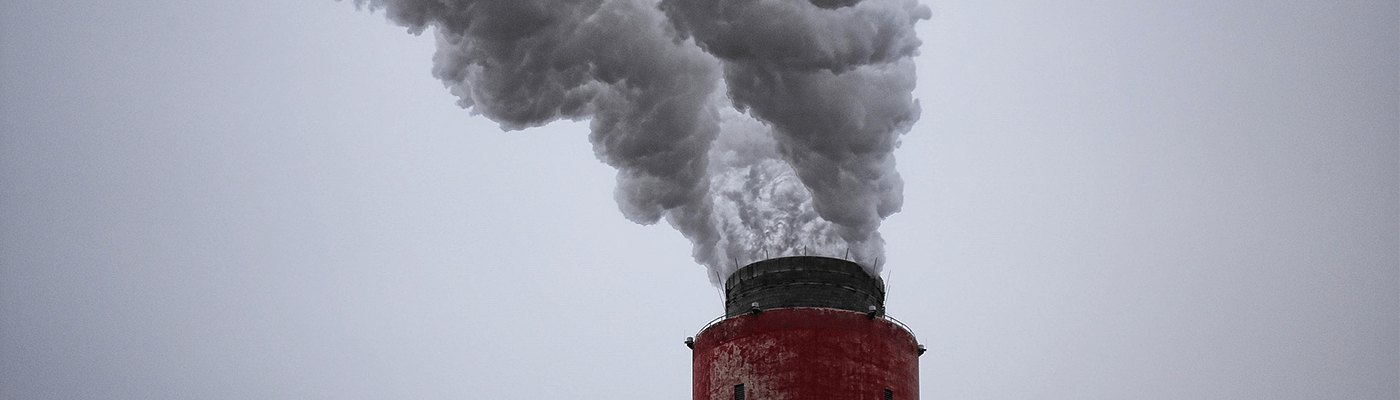
Prototype for complex flue gas treatment
Prototyping - Valorization of complex industrial waste heat
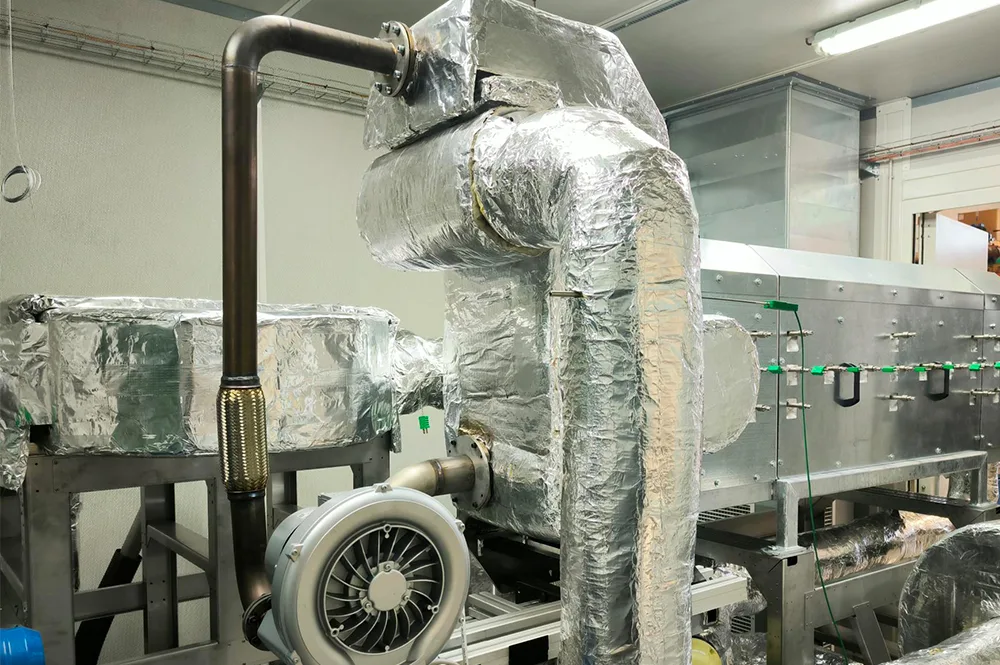
Solar power plant with mobile thermal storage
Prototyping - Mini solar power plant generating solar electricity day and night, without batteries
Development of materials from waste
Prototyping - Development of innovative ceramic materials from residues, co-products and wastes
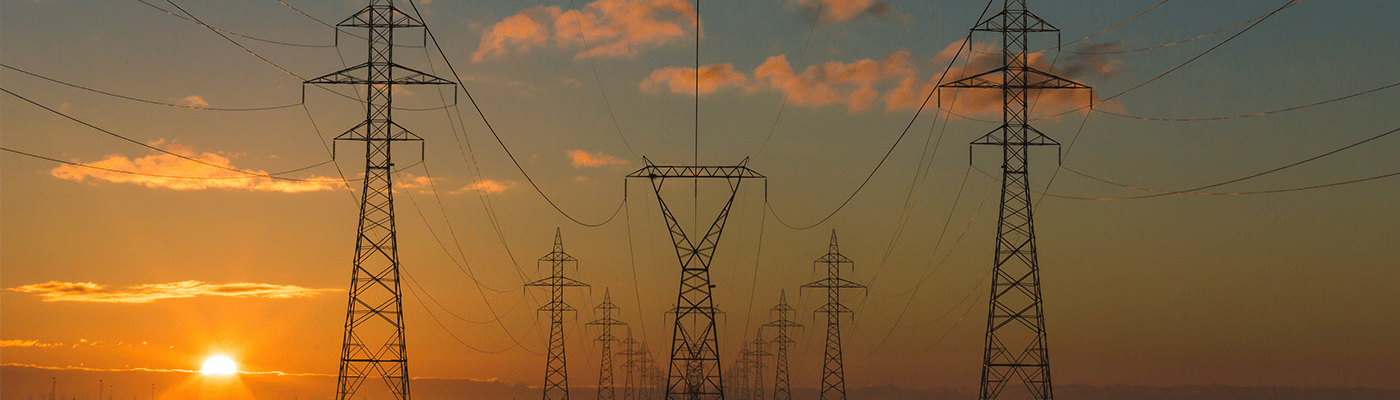
Heat and power storage in a multi-energy network
Prototyping - Optimal sizing and control of an energy network
Heat storage for solar power plants
Prototyping - Optimizing high-temperature heat storage using thermocline technology
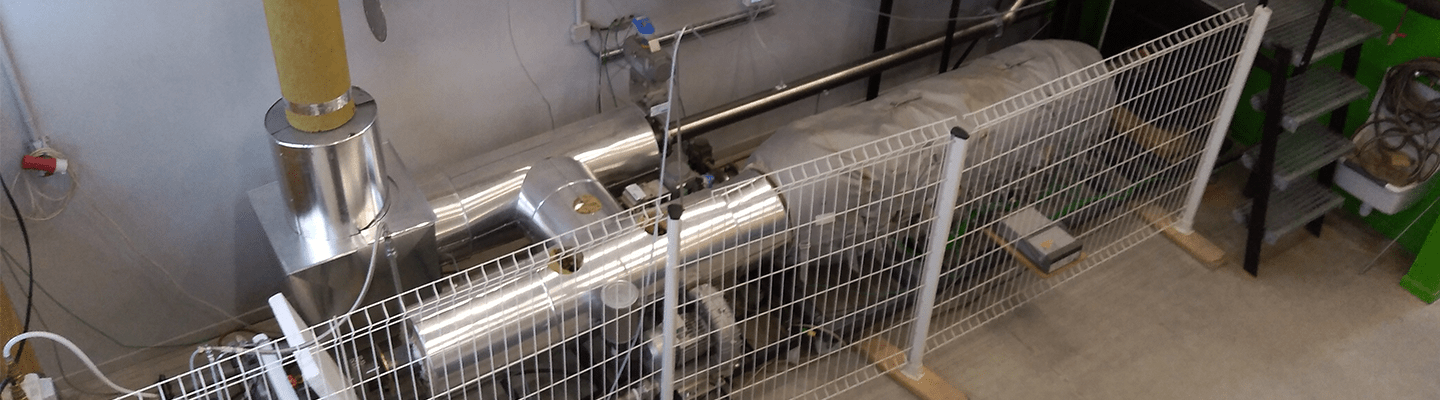
900° C thermal storage prototype, intelligent remote control
Prototyping - Production of a prototype capable of storing heat up to 900°C.
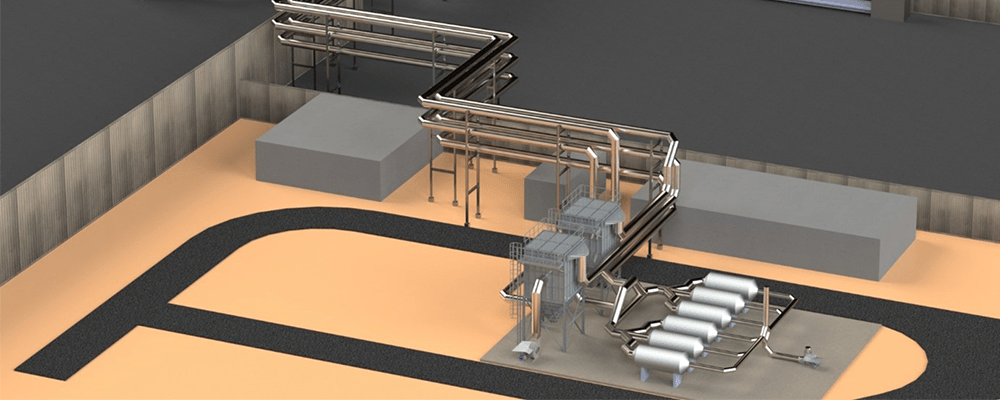
Waste heat recovery from electric arc furnaces
Metallurgy - Reduction of electric arc furnace consumption by drying the products before loading.
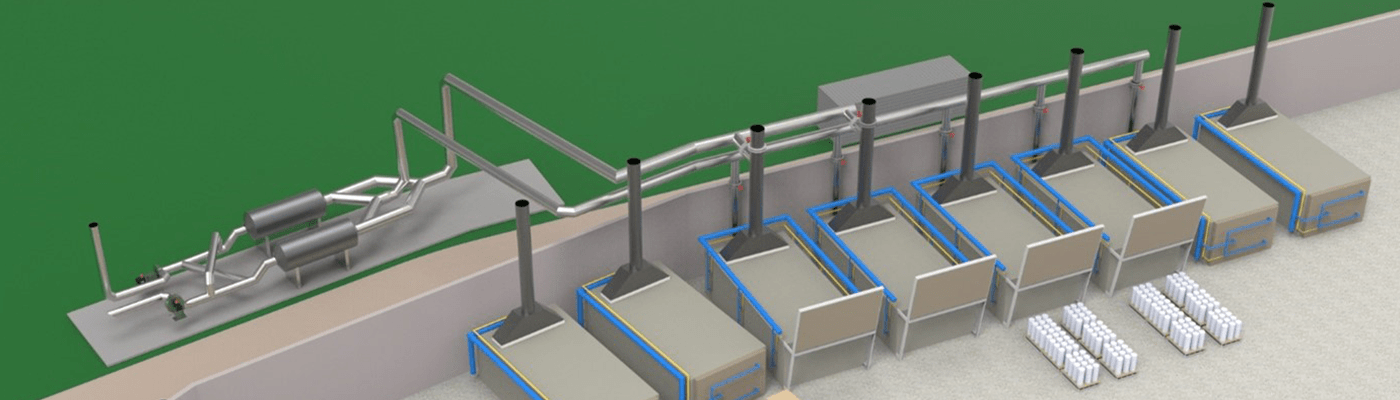
Waste heat recovery from enameling furnaces
Ceramics - Reduction of the consumption of glazing and degreasing furnaces and recovery of this energy through a high temperature storage solution.